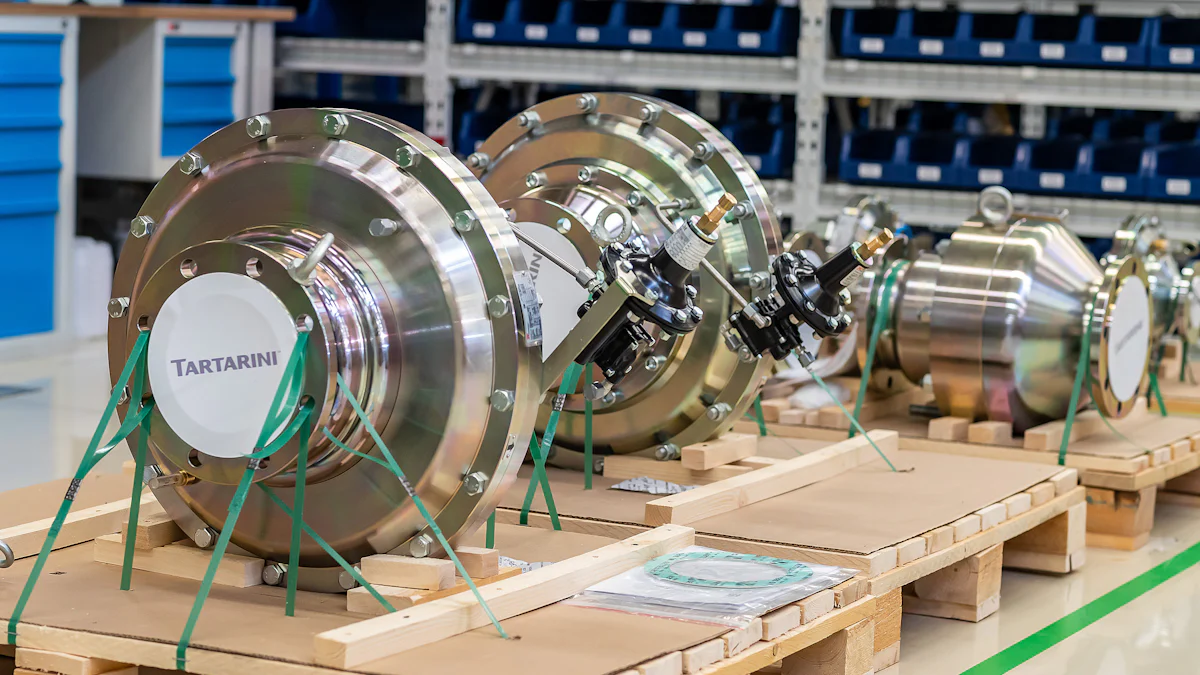
Deep groove ball bearings play a crucial role in modern machinery. These bearings, known for their versatility and efficiency, support various mechanical applications. Industries such as automotive, manufacturing, and consumer electronics rely heavily on them. Their ability to handle both radial and axial loads makes them indispensable. In North America, the market for deep groove ball bearings is thriving, holding over 40% of global revenue. This growth highlights their importance across sectors. As technology advances, the demand for these bearings continues to rise, underscoring their relevance in today’s industrial landscape.
Basics of Deep Groove Ball Bearings
Definition and Characteristics
What are Deep Groove Ball Bearings?
Deep groove ball bearings rank among the most commonly used types of bearings. Their simple design and versatility make them suitable for a wide range of applications. These bearings consist of an inner and outer ring, with a set of balls in between. The balls roll within deep grooves on the rings, allowing for smooth rotation. This design enables them to handle both radial and axial loads efficiently.
Key Features and Benefits
Deep groove ball bearings offer several key features that enhance their performance. They provide high rotational speeds due to their low friction characteristics. This makes them ideal for applications requiring rapid movement. Additionally, these bearings exhibit excellent durability and longevity. For instance, NSK Deep Groove Ball Bearings use high-quality steel, extending bearing life by up to 80%. Furthermore, they are easy to maintain, which reduces downtime in industrial settings.
Construction and Materials
Components of Deep Groove Ball Bearings
The construction of deep groove ball bearings involves several essential components. These include the inner ring, outer ring, and a cage that holds the balls in place. The cage ensures even spacing of the balls, preventing contact and reducing friction. This arrangement allows for smooth and efficient operation. The simplicity of this design contributes to the widespread use of these bearings across various industries.
Common Materials Used
Manufacturers use a variety of materials to produce deep groove ball bearings, each chosen for specific properties. High-grade steel is a common choice due to its strength and resistance to wear. For example, NTN Corporation Tenter Clip Bearing uses high-grade steel to reduce friction and improve efficiency. In environments where corrosion resistance is crucial, stainless steel or ceramic materials may be used. Customization options allow engineers to select materials that best suit their operational requirements, ensuring optimal performance and longevity.
Functionality and Mechanism of Deep Groove Ball Bearings
How Deep Groove Ball Bearings Work
Deep groove ball bearings operate by facilitating smooth rotation between two parts. They consist of an inner ring, an outer ring, and a set of balls. These balls roll within deep grooves on the rings, allowing for efficient movement. This design enables them to handle both radial and axial loads effectively.
Load Handling Capabilities
Deep groove ball bearings excel in managing various load types. They can support radial loads, which act perpendicular to the shaft. Additionally, they handle axial loads, which act parallel to the shaft. This dual capability makes them versatile for numerous applications. For instance, in automotive engines, these bearings manage the forces generated during operation, ensuring smooth performance.
Rotational Efficiency
Rotational efficiency stands as a key feature of deep groove ball bearings. Their low friction design allows for high-speed rotation. This efficiency reduces energy consumption and enhances performance. In electric motors, for example, these bearings enable rapid movement with minimal resistance. This characteristic proves essential in applications requiring quick and precise motion.
Types and Variations of Deep Groove Ball Bearings
Deep groove ball bearings come in various types, each suited for specific needs. Understanding these variations helps in selecting the right bearing for a particular application.
Single Row vs. Double Row
Single row deep groove ball bearings feature one set of balls. They offer simplicity and are suitable for applications with moderate load requirements. In contrast, double row bearings contain two sets of balls. This design increases load capacity, making them ideal for heavy-duty applications. For instance, industrial machinery often uses double row bearings to handle substantial forces.
Sealed vs. Open Bearings
Sealed deep groove ball bearings come with protective seals. These seals prevent contaminants from entering the bearing, enhancing durability. They require less maintenance, making them suitable for environments with dust or moisture. Open bearings, on the other hand, lack seals. They allow for easy lubrication but may require more frequent maintenance. Engineers choose between sealed and open bearings based on environmental conditions and maintenance preferences.
Applications of Deep Groove Ball Bearings in Various Industries
Deep groove ball bearings find extensive applications across various industries due to their versatility and efficiency. Their ability to handle both radial and axial loads makes them indispensable in many sectors.
Automotive Industry
Use in Engines and Transmissions
In the automotive industry, deep groove ball bearings play a crucial role in ensuring the smooth operation of engines and transmissions. These bearings support the crankshaft and camshaft, allowing for efficient rotation and reducing friction. This efficiency leads to improved fuel economy and reduced emissions. By minimizing wear and tear, they extend the lifespan of engine components, contributing to overall vehicle reliability.
Role in Wheel Assemblies
Deep groove ball bearings are also vital in wheel assemblies. They provide the necessary support for wheels, enabling smooth and stable movement. This stability enhances vehicle handling and safety. In addition, these bearings help reduce noise and vibration, improving the driving experience. Their durability ensures long-lasting performance, making them a preferred choice for automotive manufacturers.
Industrial Machinery
Application in Conveyor Systems
In industrial settings, deep groove ball bearings are essential components of conveyor systems. They facilitate the smooth movement of conveyor belts, ensuring efficient material handling. These bearings withstand heavy loads and harsh conditions, maintaining performance over time. Their low maintenance requirements make them cost-effective solutions for industries seeking to optimize operations and reduce downtime.
Use in Electric Motors
Electric motors rely on deep groove ball bearings for efficient operation. These bearings support the motor shaft, allowing for high-speed rotation with minimal friction. This efficiency translates to energy savings and enhanced motor performance. By reducing heat generation, they prevent overheating and extend motor life. Industries benefit from the reliability and longevity of these bearings in various applications.
Consumer Electronics
Bearings in Household Appliances
Deep groove ball bearings are integral to household appliances, such as washing machines and refrigerators. They enable smooth and quiet operation, enhancing user comfort. These bearings support rotating components, reducing wear and prolonging appliance life. Their compact design fits seamlessly into small spaces, making them ideal for modern appliances that prioritize efficiency and performance.
Role in Computer Hardware
In computer hardware, deep groove ball bearings ensure the smooth functioning of cooling fans and hard drives. They allow for rapid fan rotation, preventing overheating and maintaining optimal performance. In hard drives, these bearings support the spindle, enabling precise data reading and writing. Their reliability and low noise levels make them suitable for sensitive electronic equipment.
Market Insights: According to a Deep Groove Ball Bearings Market Business Report, the market for these bearings is expanding due to their cost-effectiveness and performance balance. Industries benefit from increased efficiency and cost savings, as highlighted in various case studies.
Advantages and Limitations of Deep Groove Ball Bearings
Benefits of Using Deep Groove Ball Bearings
Durability and Longevity
Deep groove ball bearings stand out for their durability and longevity. Manufacturers design these bearings to withstand extensive use, making them a reliable choice for various applications. The robust construction ensures that they can endure high-speed operations without significant wear and tear. This durability translates into a longer lifespan, reducing the need for frequent replacements. Industries benefit from this reliability, as it minimizes downtime and maintenance costs.
Cost-Effectiveness
The cost-effectiveness of deep groove ball bearings makes them a preferred option in many sectors. Their simple design and efficient performance contribute to lower production costs. Additionally, their ability to handle both radial and axial loads reduces the need for multiple bearing types, further cutting expenses. The low friction motion of these bearings enhances energy efficiency, leading to cost savings in operational settings. Companies appreciate the balance between performance and affordability that these bearings offer.
Potential Drawbacks
Limitations in Load Capacity
Despite their advantages, deep groove ball bearings have limitations in load capacity. While they excel in handling both radial and axial loads, they may not support as significant a radial load as roller bearings. This limitation can restrict their use in applications requiring heavy load support. Engineers must carefully assess the load requirements of their machinery to determine if deep groove ball bearings are suitable. In cases where higher radial loads are necessary, alternative bearing types might be more appropriate.
Maintenance Considerations
Maintenance considerations also play a role in the application of deep groove ball bearings. Although these bearings require less maintenance than some alternatives, they still need regular inspection and lubrication to ensure optimal performance. In environments with high contamination levels, sealed bearings might be necessary to prevent debris from affecting operation. However, sealed bearings can limit the ease of lubrication, requiring careful planning for maintenance schedules. Understanding these considerations helps industries maintain the efficiency and longevity of their equipment.
Deep groove ball bearings hold significant importance in various industries due to their versatility and efficiency. They support both radial and axial loads, making them essential in automotive, industrial, and consumer electronics sectors. As technology advances, the demand for these bearings will likely increase. Future trends may focus on enhancing their durability and performance. Industries will continue to rely on deep groove ball bearings for their cost-effectiveness and reliability. Understanding their applications and benefits can help businesses optimize machinery and improve operational efficiency.
Post time: Nov-01-2024