Step-by-Step Guide to Using Cylindrical Roller Bearings
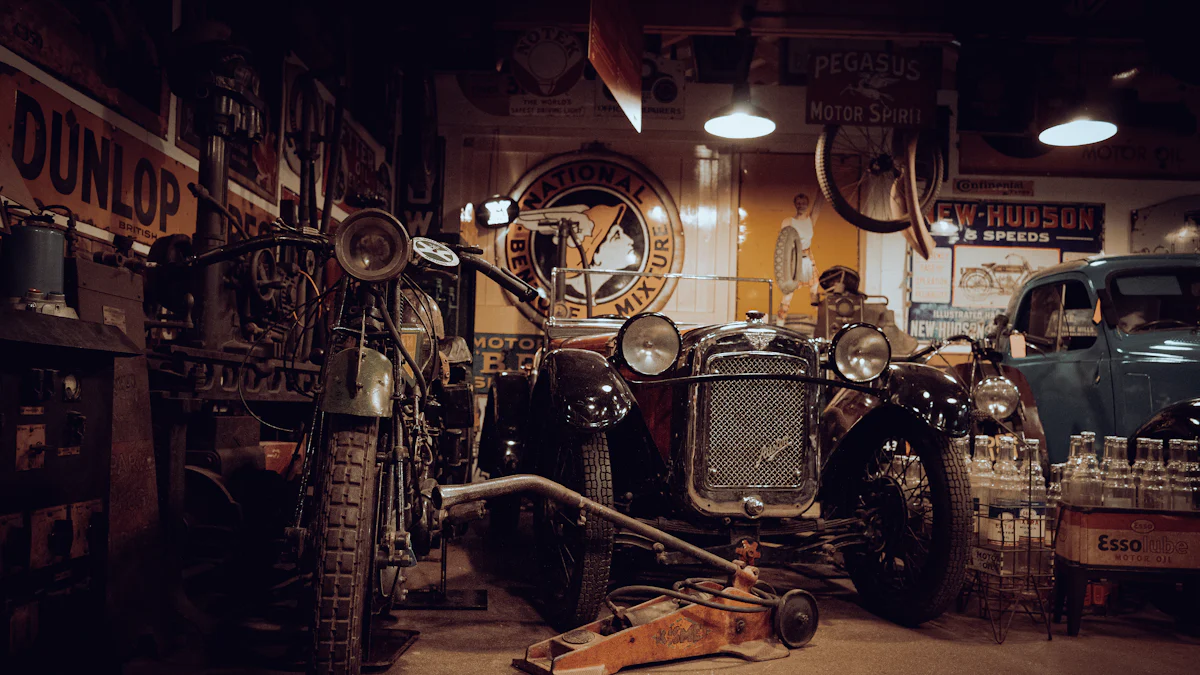
Cylindrical roller bearings play a crucial role in many industries. These bearings handle heavy radial loads and operate efficiently at high speeds. You will find them in applications ranging from industrial machinery to automotive components. The global market for cylindrical roller bearings continues to grow, driven by their versatility and reliability. This guide aims to help you understand how to use these bearings effectively, ensuring optimal performance and longevity in your applications.
Understanding Cylindrical Roller Bearings
What are Cylindrical Roller Bearings?
Basic definition
Cylindrical roller bearings are mechanical components designed to handle heavy radial loads. They consist of cylindrical rollers that make linear contact with the raceways, allowing them to support high-speed applications efficiently. You will find these bearings in various industries due to their ability to manage substantial loads with minimal friction.
Historical background
The development of cylindrical roller bearings dates back to the early 20th century. Engineers sought to improve machinery efficiency by reducing friction between moving parts. Over time, advancements in materials and manufacturing techniques have enhanced the performance and reliability of these bearings, making them indispensable in modern industrial applications.
Components of Cylindrical Roller Bearings
Inner and outer rings
The inner and outer rings form the primary structure of a cylindrical roller bearing. These rings provide the raceways for the rollers, ensuring smooth rotation and load distribution. The precision of these rings is crucial for the bearing’s overall performance and longevity.
Rollers and cage
The rollers in a cylindrical roller bearing are cylindrical in shape, allowing them to distribute loads evenly across the raceways. A cage holds these rollers in place, maintaining their alignment and preventing contact between adjacent rollers. This design minimizes friction and wear, enhancing the bearing’s efficiency and lifespan.
Types of Cylindrical Roller Bearings
Single row
Single row cylindrical roller bearings are the most common type. They consist of a single row of rollers, providing high radial load capacity while maintaining a compact design. These bearings are suitable for applications where space is limited, yet high performance is required.
Double row
Double row cylindrical roller bearings feature two rows of rollers, offering increased load capacity compared to single row designs. You might choose this type when dealing with heavier loads or when additional stability is necessary. Their robust construction makes them ideal for demanding industrial environments.
Multi-row
Multi-row cylindrical roller bearings contain multiple rows of rollers, significantly enhancing their load-bearing capabilities. These bearings are used in applications where extreme loads are present, such as in heavy machinery and construction equipment. Their design ensures optimal performance under the most challenging conditions.
Advantages and Disadvantages
Understanding the advantages and disadvantages of cylindrical roller bearings helps you make informed decisions for your applications. These bearings offer several benefits, but they also come with certain limitations.
Advantages
High load capacity
Cylindrical roller bearings excel in handling heavy radial loads. Their design features cylindrical rollers that provide a larger contact area with the raceways. This structure allows them to distribute loads more evenly compared to other types of bearings, such as ball bearings. You will find these bearings particularly useful in applications where high radial load capacity is essential, like in industrial machinery and gearboxes.
Low friction
The design of cylindrical roller bearings minimizes friction between moving parts. The rollers make linear contact with the raceways, reducing the frictional forces that can slow down machinery. This low friction characteristic enhances the efficiency of your equipment, leading to smoother operation and reduced energy consumption. In high-speed applications, this advantage becomes even more pronounced, allowing for optimal performance.
Disadvantages
Limited axial load capacity
While cylindrical roller bearings are excellent at handling radial loads, they have limited capacity for axial loads. The design focuses on supporting loads perpendicular to the shaft, which means they might not perform well in applications requiring significant axial load support. You should consider this limitation when selecting bearings for your machinery, especially if axial loads are a factor.
Sensitivity to misalignment
Cylindrical roller bearings are sensitive to misalignment. Proper alignment is crucial for their optimal performance. Misalignment can lead to uneven load distribution, increasing wear and reducing the lifespan of the bearing. You must ensure precise installation and regular maintenance to prevent misalignment issues. This sensitivity requires careful attention during setup and operation to maintain the bearing’s efficiency and longevity.
Selection Criteria
Choosing the right cylindrical roller bearings involves understanding several key factors. This section will guide you through the essential criteria to consider for optimal performance.
Load Requirements
Radial load
Cylindrical roller bearings excel in handling high radial loads. You should assess the radial load requirements of your application. These bearings distribute loads evenly across their linear contact areas, making them ideal for heavy-duty applications. Ensure that the bearing you select can support the radial forces present in your machinery.
Axial load
While cylindrical roller bearings primarily handle radial loads, they have limited axial load capacity. You need to evaluate the axial load demands of your application. If significant axial loads are involved, consider additional support or alternative bearing types. Proper assessment ensures that the bearing performs efficiently without premature failure.
Speed and Temperature Considerations
Operating speed
Cylindrical roller bearings are suitable for high-speed applications. You should determine the operating speed of your machinery. Bearings designed for high speeds minimize friction and heat generation, ensuring smooth operation. Select a bearing that matches the speed requirements to prevent overheating and wear.
Temperature range
Temperature affects bearing performance. You must consider the operating temperature range of your application. Some cylindrical roller bearings, like the ET Series, support continuous operation from -40 to 120°C. Choose a bearing that withstands the temperature extremes in your environment to maintain reliability and longevity.
Environmental Factors
Corrosion resistance
Environmental conditions impact bearing selection. You should evaluate the potential for corrosion in your application. Bearings with corrosion-resistant materials or coatings offer enhanced durability. This feature is crucial in environments exposed to moisture or chemicals, ensuring the bearing’s extended service life.
Dust and contamination
Dust and contamination pose risks to bearing performance. You need to assess the cleanliness of your operating environment. Bearings with effective sealing mechanisms protect against contaminants, reducing wear and extending lifespan. Consider these factors to ensure your bearings operate efficiently and with minimal maintenance.
Applications of Cylindrical Roller Bearings
Cylindrical roller bearings find extensive use across various industries due to their ability to handle heavy radial loads and operate efficiently at high speeds. You will encounter these bearings in both industrial machinery and the automotive industry, where their reliability and performance are crucial.
Industrial Machinery
In industrial settings, cylindrical roller bearings play a vital role in ensuring the smooth operation of machinery. Their design allows them to support substantial loads, making them indispensable in several applications.
Gearboxes
Gearboxes rely heavily on cylindrical roller bearings to manage the radial loads generated during operation. These bearings provide the necessary support to ensure that gearboxes function efficiently, reducing wear and extending the lifespan of the machinery. By using cylindrical roller bearings, you can enhance the performance and reliability of gearboxes, which are critical components in many industrial machines.
Electric Motors
Electric motors benefit significantly from the use of cylindrical roller bearings. These bearings help maintain the motor’s efficiency by minimizing friction and supporting the radial loads encountered during operation. With their ability to handle high speeds, cylindrical roller bearings ensure that electric motors run smoothly, reducing energy consumption and maintenance needs. You will find these bearings essential in applications where electric motors drive industrial processes.
Automotive Industry
In the automotive industry, cylindrical roller bearings contribute to the performance and durability of various components. Their robust design makes them suitable for handling the demands of automotive applications.
Transmissions
Transmissions in vehicles require bearings that can withstand the stresses of operation. Cylindrical roller bearings provide the necessary support for the radial loads present in transmissions, ensuring smooth gear shifts and reliable performance. By incorporating these bearings, you can improve the efficiency and longevity of automotive transmissions, which are vital for vehicle operation.
Wheel Hubs
Wheel hubs also benefit from the use of cylindrical roller bearings. These bearings support the radial loads exerted on the wheels, ensuring stable and efficient rotation. By using cylindrical roller bearings in wheel hubs, you can enhance the safety and performance of vehicles, providing a smoother ride and reducing wear on other components.
Case Studies: Reports in the automotive and industrial engineering sectors highlight the importance of cylindrical roller bearings. These studies range from simple reviews to in-depth investigations of failed components, emphasizing the need for proper selection and maintenance of bearings.
In conclusion, cylindrical roller bearings are integral to both industrial machinery and automotive applications. Their ability to handle heavy radial loads and operate at high speeds makes them a preferred choice for enhancing the performance and reliability of various components.
Cylindrical roller bearings are vital in many industries, offering high load capacity and low friction. Proper selection and maintenance are crucial for maximizing their performance and lifespan. You must consider factors like load requirements, speed, and environmental conditions when choosing bearings. Regular maintenance prevents premature failures, which can lead to machinery breakdowns. As David Riley, a consultant engineer, emphasizes, “Bearings play a very important role in providing stiffness and rotational accuracy.” For specific applications, consulting with experts ensures you make informed decisions, enhancing the reliability and efficiency of your machinery.
Post time: Nov-01-2024